Waste Not, Want Not
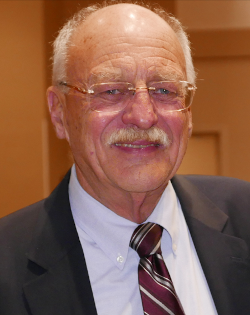
Builders Must Establish Effective
Material Controls
By: Chuck C. Shinn, Jr., Ph.D., Founder, Builder Partnerships
Direct construction costs are the largest cost classification for builders, typically representing between 50 and 65 percent of the sales price. Direct costs are referred to as variable costs; in other words, builders do not incur the cost unless they build a home, therefore it has a multiplier effect. If builders can reduce their direct construction (material) costs by $1,000 per home and build and sell 100 homes, builders can add $100,000 to their net profits.
As I visit job sites, I constantly see profits left lying on the ground or thrown out with the trash. I find excess material lying around the job site, misused material, excess material being installed or left on job site, and poor material handling and protection during delivery and after installation. It is not unusual for me to see 10 extra sheets of drywall sitting exposed to the weather in the garage, several bundles of roofing thrown off the roof, etc. This poor material control leads to a substantial amount of lost profits.
As a manufacturer, you can help your builder clients manage construction costs by providing them with guidelines on how to obtain efficiencies on installations and how to better protect materials during construction. With today's ever-increasing prices and material shortages, you can stand out from your competition, build trust, and gain loyalty by helping builders overcome these challenges.
Posted On 2021-05-30 | Articles